Project Case Studies
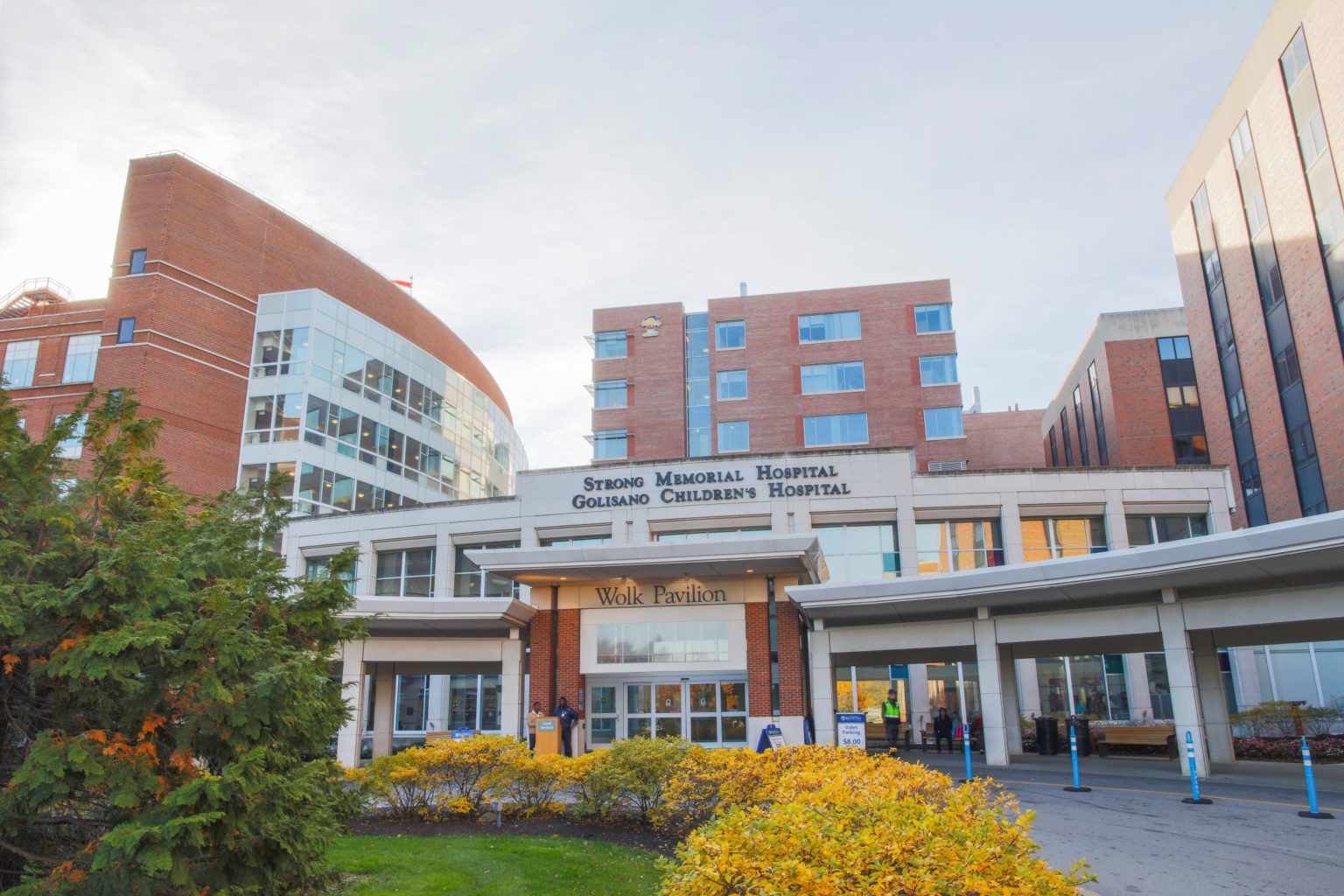
University of Rochester Medical Center
Master Transport Study and Campus Logistics Master Plan.
An analysis and Master Plan for Materials and Waste Management, Food and Nutrition Services, Linen, Sterile Processing and everything requiring movement within an existing facility with plans for major expansion. We then provided designs and management engineering services based on the Master Plan
Objectives.
The existing URMC Strong Memorial Hospital (SMH) was designed in the late 1960’s and constructed in the early 1970’s with the understanding that all of its various transportation systems would be retained and maintained as fully operational as the facility aged. The original designs included a number of systems that, at that time, were truly “state of the art” and provided very safe, efficient and reliable movement of everything that needed to move. Transport systems included: passenger and patient service elevators, a comprehensive pneumatic tube system and an overhead rail cart transport system.
Together they transported the many 1000’s of: people, clean and soiled materials carts, medications, specimens, devices, etc. that supported the daily healthcare goals of the University of Rochester Medical Center. Together these systems performed well and helped SMH meet its goals, objectives and obligations to the community. Over time new buildings and functions were added, increasing and changing flows of people, clean and soiled materials and equipment. Planning must also support new major additions such as that being planned.
In addition to these transport systems were the various support services such as Food and Nutrition Services, Materials and Waste Management, Linen Services and Central Sterile Processing that were sized and located to support the original SMH but were not designed to consider the loadings of the subsequent additions such as the new Ambulatory Care Center and Cancer Treatment Center. These additions created demands on the ability of the existing departments to provide support and also manage the greater distances involved. Where these support services were proximate to the original Using departments the new buildings had to be constructed, due to site conditions, many 100’s of feet further away from their supporting departments.
As might be expected, the elevators, pneumatic tube and the Overhead Rail transport systems have degraded over time due to many reasons and their capabilities have been diminished. The elevators and the pneumatic tube system have been well maintained but as they age even proper maintenance is not able to keep them as reliable as they need to be to adequately support SMH. These systems however can be modernized in place. The Overhead Rail Automated Cart Transport System (ACTS), which had been designed to last up to 25 years, continues to operate through nothing short of heroic efforts by the facility’s engineering staff, but as spare parts have become almost impossible to find it has reached the end of its practical life. The ACTS, which had previously moved about 2,000 carts each day can now handle only about 500 to 600, leaving the movement of ~1,400 carts to be transported by the Service Elevators which were not meant to handle that traffic. Compounding these issues are the changes in healthcare requirements, new building additions, increased populations and the changes to URMC traffic flows over the past 35 years.
Implementation.
The Schachinger Group (TSG) was retained by the University of Rochester Medical Center (URMC) to conduct a Master Transport and Logistics Study for the SMH campus as a basis for a Materials Management / Logistics Master Plan to augment the Campus Facility Master Plan. A primary purpose of the study was to inspect and analyze the existing VT and MH transport systems to identify and quantify: performance, physical condition and their specific capabilities in safely, efficiently and reliably moving patients, staff, visitors, materials, wastes, and equipment. Detailed data collection and operational and physical reviews and recommendations were made for the Support Departments. As a result of these studies, TSG provided detailed recommendations that will dramatically improve current and projected future vertical and horizontal circulation for the campus, with better efficiencies, reductions in operating costs and improvements in moral and the Hospital’s community image. URMC recognizes that operational efficiencies will dramatically increase.
VERTICAL TRANSPORT SYSTEMS
TSG performed detailed elevator usage studies and technical evaluations of the existing vertical transport systems (passenger, service and freight elevators) to assess the physical and operational condition, determine the actual needs, and reveal potential options for improvement. It was determined that improved systems would provide more capacity for pedestrian traffic, including the ever critical patient transports, on the existing vertical transport systems. Results of the Elevator Usage Survey demonstrated that several of the existing passenger and service elevator cores were vastly
underperforming to even a ‘fair’ rated standard. TSG then provided the recommendations for the work to be accomplished. The end result is a more than doubling of the handling capacity of the vertical transport systems while reducing waiting times for patients and passengers by over 40% for the peak travel periods.
MATERIALS HANDLING SYSTEMS
A significant part of TSG’s work was to perform a comprehensive physical and functional assessment of the facilities existing materials handling systems and equipment which include: the overhead rail system, pneumatic tube system, dumbwaiters and chutes. This assessment included traffic studies to identify existing people and materials flows within the hospital to determine entry points, volumes, and pathways and operational procedures and an analysis and development of recommendations.
The Overhead Rail System (ORS), installed in 1972, was originally designed to handle all bulk material transport functions. Horizontal paths are in the buildings sub basement with vertical connections to User and Support departments. Due to the degradation of the ORS, the system now only handles trash, medical waste, and soiled linen carts, and the facility utilizes the existing elevator system for all other Materials Handling Transport. TSG provided a detailed report outlining the impact on both the Vertical Transport Systems and the Materials Handling Systems in the event of an Overhead Rail System shut down, planned and unplanned. The report included recommendations for both long and short term actions to minimize the impact on facility circulation including a planned replacement of the ORS by an AGVS. Final results will increase operating efficiencies by over 100% and removing the materials from service elevators will greatly improve patient, staff and visitor transportation.
MATERIALS AND WASTE MANAGEMENT, CSSD SYSTEMS
Management engineering and operational programming, along with departmental redesigns will be accomplished as Phase 2 of this engagement and is expected to substantially improve efficiencies and decrease operating costs.
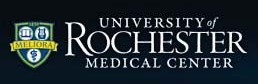
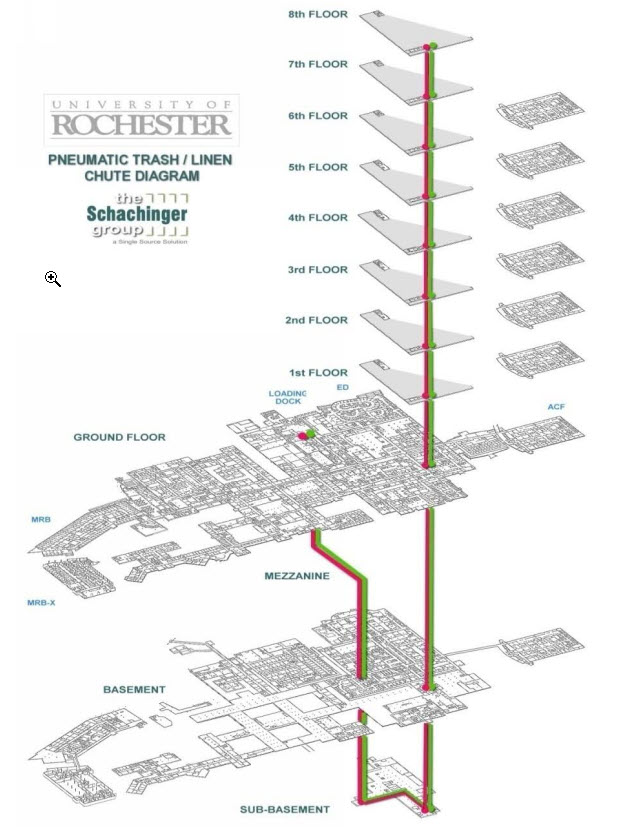
Fig. 1
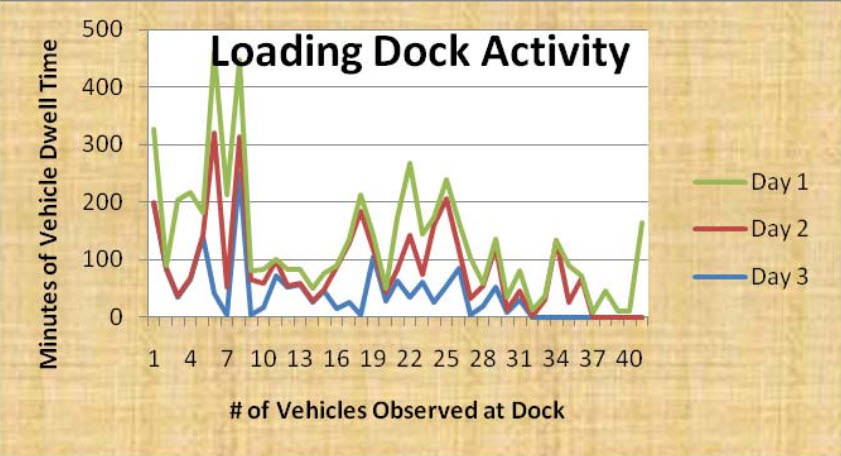
Fig. 2
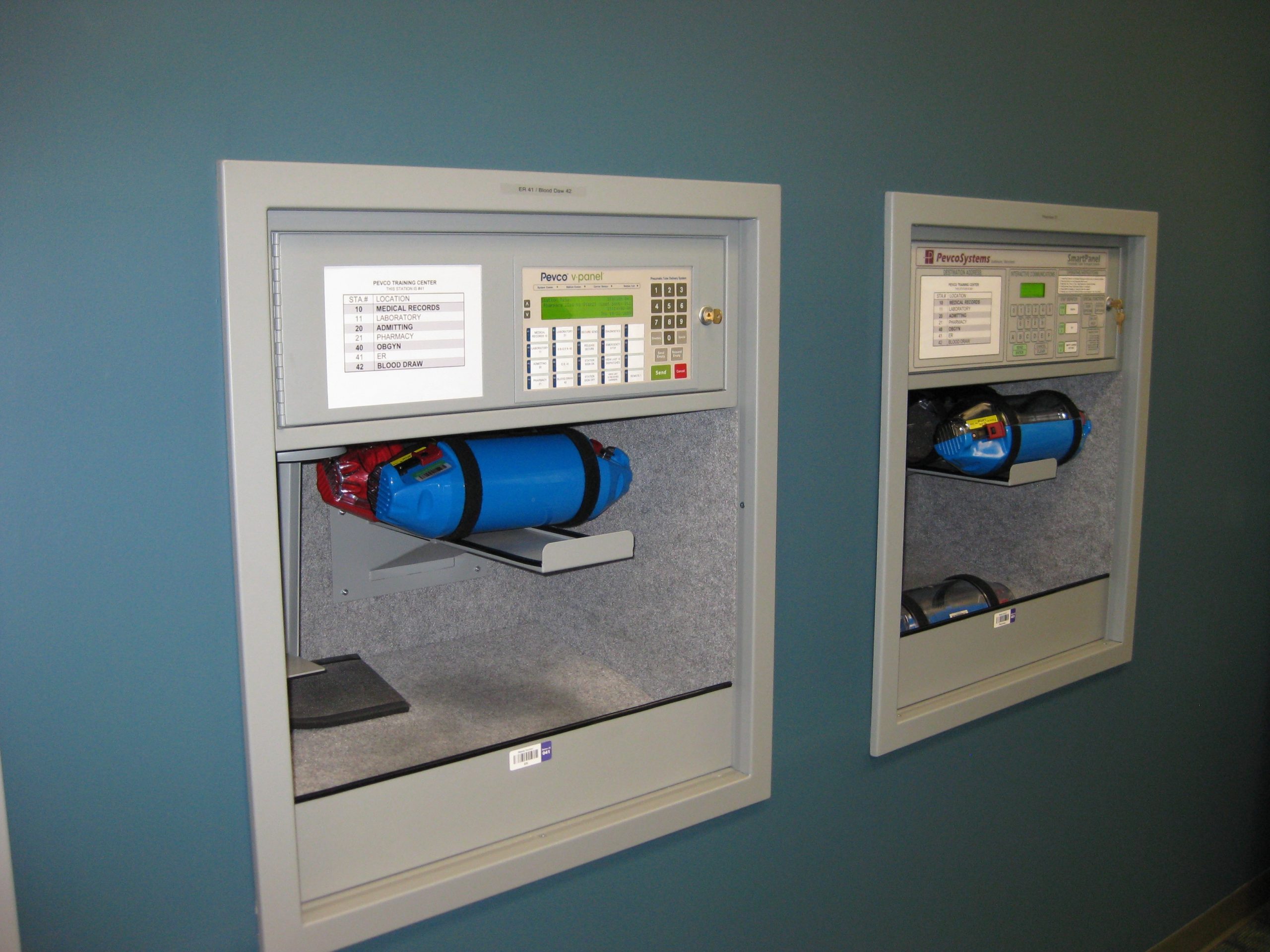
Fig. 3
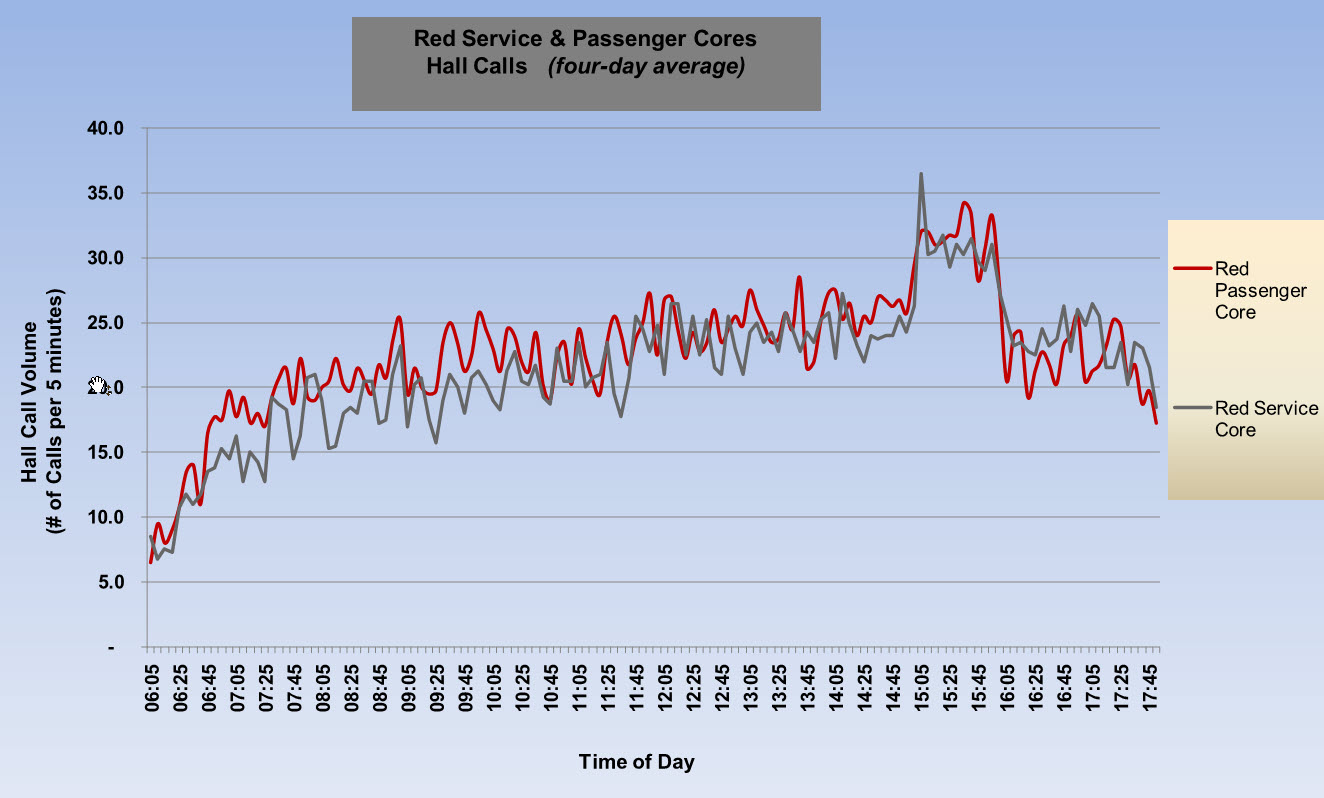
Fig. 4
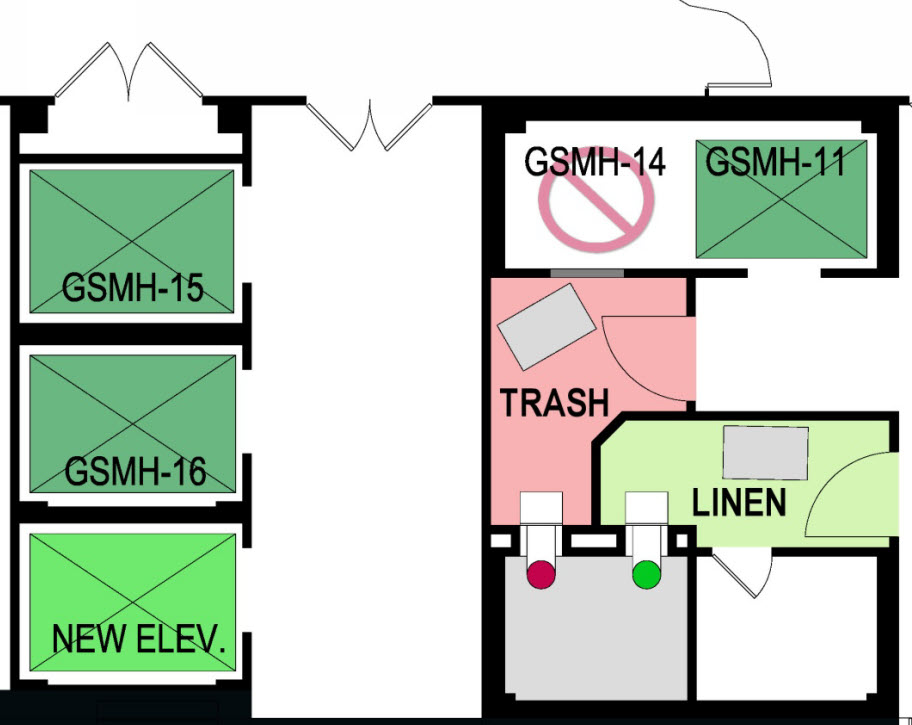
Fig. 5
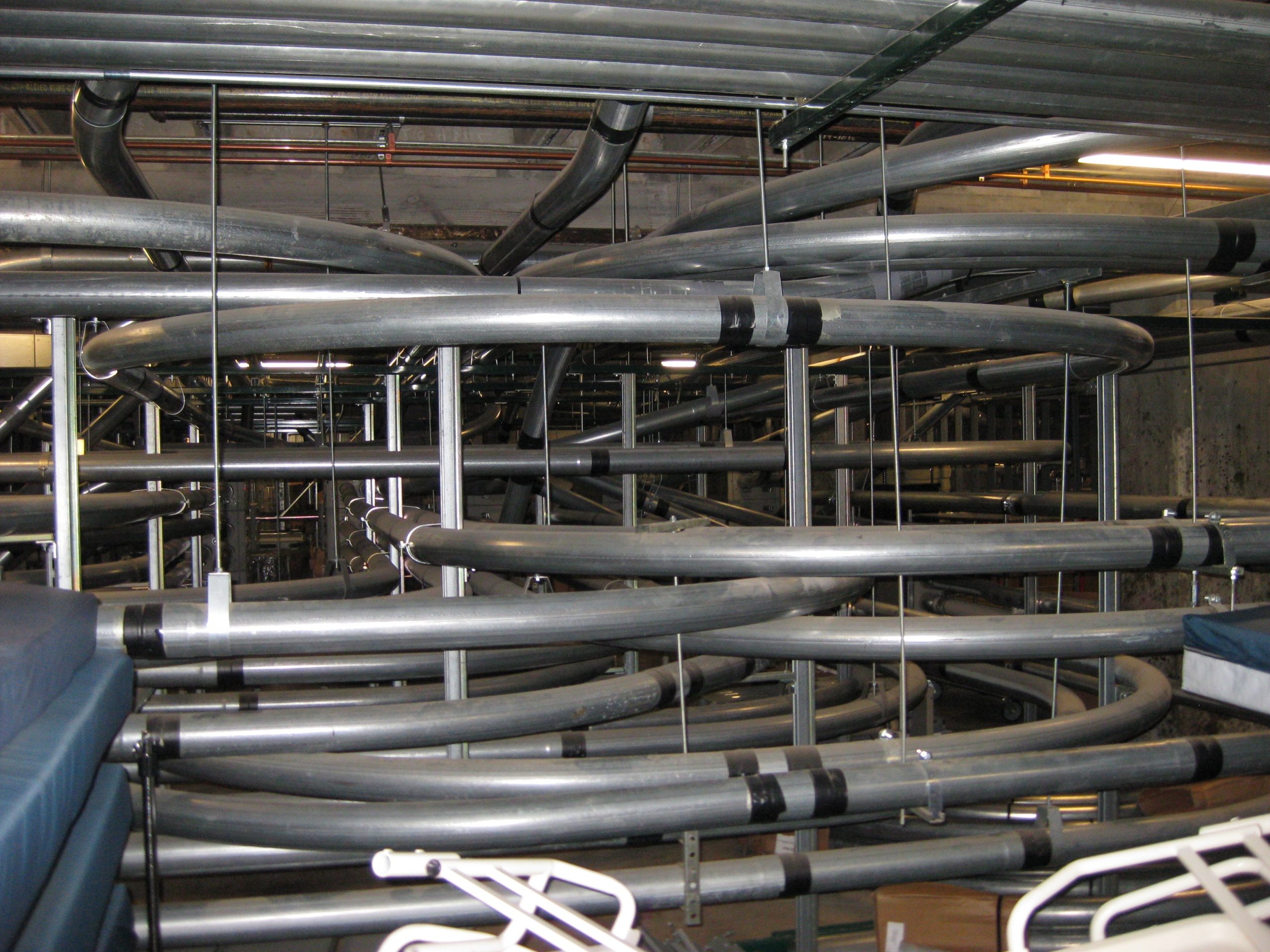
Fig. 6
Contact The Schachinger Group. (703) 608-2263
Our experience in providing services for more than 800 clients worldwide over 35 years has revealed the benefits of treating these important disciplines as interdependent functions, planned in a coordinated way with the assistance of one experienced and qualified firm.