Project Case Studies
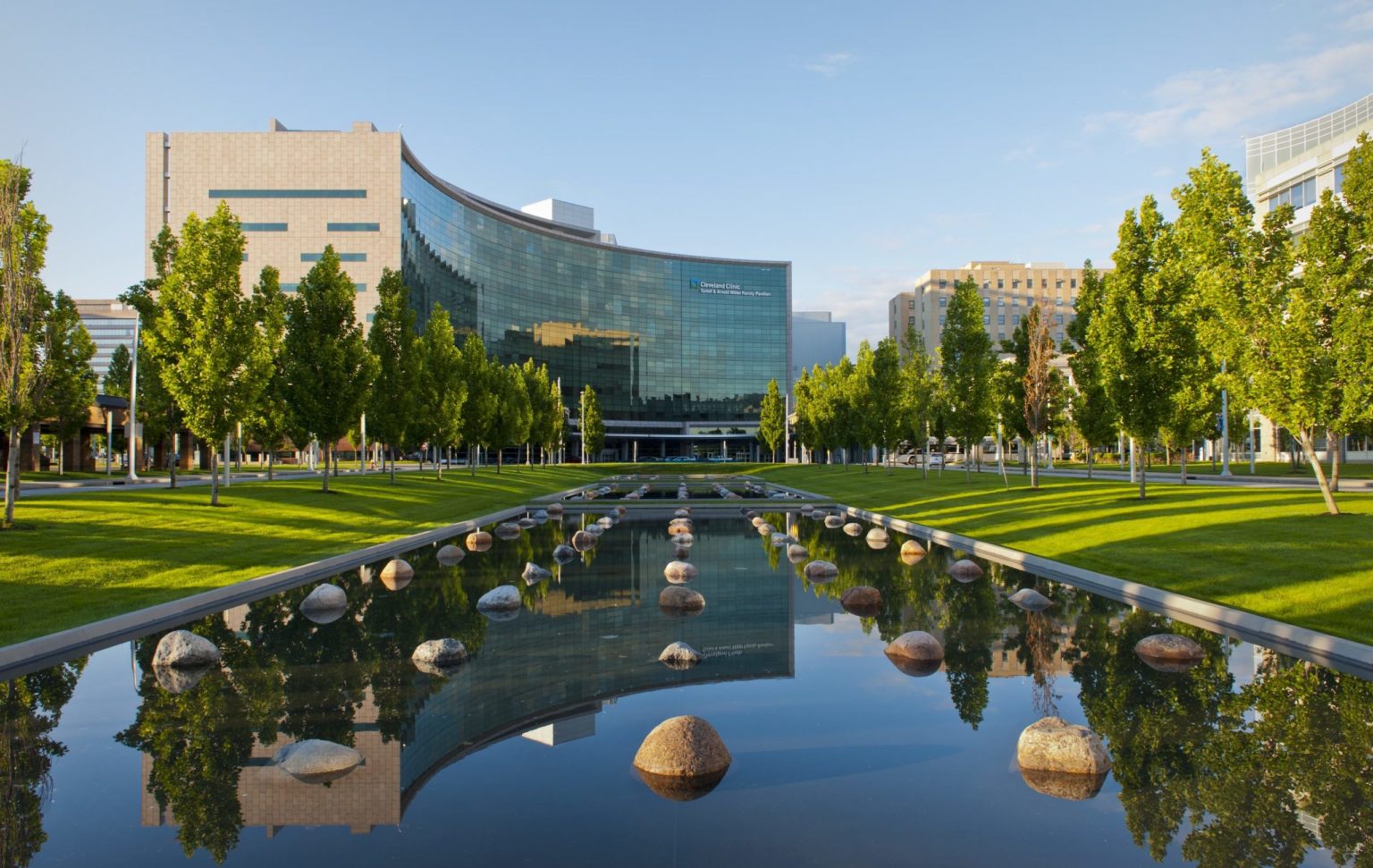
Cleveland Clinic Projects.
Clinic Services & AGV Robotics Group + Miller Heart Health Hospital
Project Details.
- VISIONING: The Schachinger Group (TSG) staff worked with Cleveland Clinic Foundation (CCF) staff to determine the future patient care goals of the facility, and what the CCF’s Support Services should look like: 1 year, 5 years, 10 years and 20 years in the future. TSG’s visioning process brought together the various departments to share their history, values, needs, assets and goals in order to develop a common view of their combined future. Goals were set; paths defined and the process moved forward.
- PROGRAMMING AND BUDGETING: The Schachinger Group (TSG) provided, through our experience and unique computer based tools, the functional programs, space programs and equipment lists for the Cleveland Clinic Service Center and its departments. Our specialized capabilities provided what proved to be very accurate space requirements even though there were no base lines for a facility of this type. Equipment selections and capabilities have also proven themselves appropriate in operation. TSG budgets, established early in the process, were in total, within 3% of the final acquisition costs for equipment and systems.
- INTEGRATION: The Schachinger Group (TSG) was tasked with the studies, concepts, designs, development and implementation of integrated designs and operations for the services to be housed within the new Service Center and their extension to the User Departments. The final concepts provide a single floor design with a partial mezzanine covering ~183,000 ft². All of the varied functions and operations are physically integrated through proper adjacencies and operationally through extensive use of LAN and software systems, Wi-Fi web based supply / transport tracking and signature capture. Transportation is primarily through the use of an AGVS robotic transport system.
- MANAGEMENT ENGINEERING: To avoid continuing the inefficient operations spawned in the old and undersized work spaces, The Schachinger Group (TSG) worked with Cleveland Clinic Foundation (CCF) Managers to reengineer and make more efficient the various operations and functions for the support departments. CCF eliminated “silos” and old “work arounds” replacing them with well considered functions and activities supported by the new designs and suitable for the sustainable practices and disciplines realized through the automation provided.
- SUSTAINABLE DESIGN: The design process was a closely coordinated work effort between The Schachinger Group, Inc. responsible for designing the departments, equipment and systems and the Bostwick Design Partnership designing the building elements, the parking structure and also coordinating the MEP and IT efforts. The designs closely followed the Functional and Space Programs and were closely monitored and reviewed by the Cleveland Clinic Project Team. The goal for the designs were to produce a facility that was at the leading edge of proven technology and one that would provide cost efficient service for 20 plus years.
- IMPLEMENTATION AND TRAINING: The Schachinger Group worked with Cleveland Clinic Foundation (CCF) and the systems and equipment contractors to develop, schedule and implement the detailed training programs, materials and tools required by Cleveland Clinic Foundation (CCF) staff to learn how to work successfully with the new concepts and equipment. TSG also worked with Cleveland Clinic Foundation (CCF) and their Vendors on a “hands on” basis for over four months assisting in the startup, training and implementation tasks. During the peak three week startup period TSG provided six full time “implementation” staff providing 24/7 implementation coverage.
Passenger, Material, Service Elevators, Vertical Transport
- VERTICAL TRANSPORT: Passenger, Service and Materials Elevators were studied and designed by TSG for the Cleveland Clinic Service Center and the Parking Garage. The 89th Street Garage and Service Center is equipped with five 4,000 #, 350 fpm MRL traction passenger elevators, two roped hydraulic service elevators and three forklift/freight lifts.
Materials Handling AGVS Robotic Systems.
- MATERIALS HANDLING: The Schachinger Group studied numerous MH alternatives, including: manual transport, electric tugs and tuggers, platform vehicles, Automated Guided Vehicles, various Robotic Systems, etc. for materials transport between the Cleveland Clinic Campus and the Service Center. Study results supported the implementation of an Automated Guided Vehicle System (AGVS). The AGVS utilizes 81 automated transporters and over 1,000 carts to make up the 4,800 cart moves that will be required to serve the final 1,400 bed build-out. The daily transports cover a distance of over 1,000 miles. The AGV robots will transport clean and soiled materials such as supplies, linens, wastes, food, sterile instruments, pharmaceuticals, medical equipment and other items.
AGVS ROBOTIC SYSTEMS: First of a kind unique carts designed by TSG, provide for safe AGV transport of unusual items such as commodes, crash carts and other special devices. Special controls allow for fully automated supply cart dispatch and empty waste and soiled linen cart storage, retrieval and dispatch management. An integrated Pocket PC system allows staff and management to view system conditions, delivery data such as the location of specific loads and for alerts and notification of system faults and alarms.
Cart Washer AGVS Robotic Systems
- CARTWASHING: The AGVS provides completely automated interfaces for cart washing in two fully automated cartwashers that wash, rinse and dry up to 40 carts an hour. These two units provide an unattended, centralized cart cleaning function for ALL departments including EVS and FNS. This functional and physical integration eliminates the need for separate machines in each department while providing better control and backup 24 hours / day.
Materials Management
- MATERIALS MANAGEMENT: The Cleveland Clinic maintains ~ 3,000 SKU’s in stock and manages up to an additional 100,000 non stock items. To manage and process these materials the new Cleveland Clinic Service Center uses a combination of state of the art highly sophisticated and integrated: Receiving, Warehouse Management System (WMS) and an Order Fulfillment System (OFS) fully integrated into the ERP and local automated data collection devices. The OFS will process materials with order picking rates up to eight times faster and with inventory levels approximating 40% of previous equivalent operations.
Warehouse Management System
- THE WAREHOUSE MANAGEMENT SYSTEM (WMS): is fully integrated with the ERP and will maintain real time inventories, track materials and direct picking and put away operations. Order Fulfillment is accomplished with the assistance of sophisticated “pick-to-light and “pick-to-display” systems working with pallet and carton flow racks and seven horizontal carousels. Materials are placed into tote boxes, or if picked in carton lots placed directly onto conveyors where they are automatically transported to various zones for loading, completion, consolidation and shipping. The WMS interfaces automatically with the AGVS to provide final destinations for loaded supply carts.
Non-stock items and those received through express deliveries (including Federal Express, UPS, etc.) are processed through a “fast track system” that has the capability to receive, sort, track, and deliver to its destination in two hours or less. These new efficiencies are expected to yield very substantial improvements in patient care as well as significant cost savings. - The sophisticated MM operations include “in-house” signature capture capabilities that will work in conjunction with a materials tracking system to verify the location and then final receipt of any or all materials entering the facility.
HOSPITAL SERVICE CENTER
- HOSPITAL SERVICE CENTER DOCKS: 11 high production clean truck positions and 6 soiled dock positions are providing complete access for the ~73 large truck types that must be accommodated daily. The clean receiving dock designs (by TSG) are equipped with powered levelers and doors and are capable of receiving approximately 8,000 lbs. of materials per hour per position. All clean materials are received and all soiled materials are sent from the new Service center.
The truck apron is about 30’ below ground level and has been designed to accept all truck configurations from 53’ semi’s through 20’ step vans. The truck area design allows for the various trucks to enter and exit with single direction movements and without interference with adjacent vehicles. A drive up ramp allows truck access into the building for secure deliveries and other unusual conditions. Smaller loads and deliveries that arrive in vans, cars and small trucks are managed through twenty eight (28)dedicated “materials management” positions located on the 1st floor of the Cleveland Clinic parking garage with a dedicated elevator system traveling between that area of the garage and the receiving dock levels.
- PATIENT FOOD SERVICES: A new Inpatient Food and Nutrition Services department was conceived and programmed by TSG and designed and specified by TSG’s subcontractor: Cini-Little International. The new department will provide meals for the 1,400 patients daily with the AGVS robots move all of the food carts and wastes. Food is shipped in bulk from the Food and Nutrition Services department to User floor kitchens where the food is plated and temperature conditioned. Soiled trays, utensils, plates, cups, etc. are washed at the user areas where they are used for the next meals.
- NONPATIENT FOOD SERVICES: The Cafeteria and on-site commercial restaurants receive all of their food products and supplies through the main receiving docks on special reusable pallets designed to be carried on the robotic automated guided vehicle system.
These pallets are assembled at the Contractor’s remote locations and trucked to CCF where they are loaded onto flat bed carts before transport by the AGVS. This allows the pallets to be easily moved when they arrive at their final destinations rather than require pallet jacks or other special equipment.
CENTRAL STERILE SUPPLY DEPARTMENT
- Central Sterile Supply : The new Cleveland Clinic Central Sterile Processing Department (CSSD) will process, store and distribute instruments, sterile supplies, equipment (IV pumps, commodes, etc.), crash carts and other clean and sterile materials using the robotic AGVS. Special AGVS cart designs were provided by TSG to carry the unusual shapes and conditions represented by Crash Carts, respirators and other equipment. The new CSSD contains an equipment cleaning, storage, recharging, calibration, testing and distribution function that provides these services for the various medical equipment devices for the facility.
Cleveland Clinic Textile Services
- TEXTILE SERVICES: Clean linens are produced at a remote laundry and trucked to the new Service Center where over 100 carts of clean linen will be distributed by the new AGVS on an average day. Soiled linens are collected, transported on the robotic system to the dock and returned to the remote laundry. Empty and filled soiled laundry cart storage and retrieval activities are fully managed by the AGVS with minimum attendant input.
Cleveland Clinic Waste Management
- WASTE MANAGEMENT: The core design employed a Waste Management Center concept which provided a single location for the collection, processing and disposal of all soiled materials at the Cleveland Clinic. Over 20 tons of wastes are collected, transported robotically and disposed of on an average day. The new Waste Management Center receives over 300 cart loads of soiled linen, trash, medical waste, recyclable and hazardous materials daily. All soiled cart transport, and automated storage and retrieval of clean empty carts are managed by the AGVS. Automated dumping of treated medical wastes eliminates double handling.
- AUTOMATED WASTE STERLIZERS: Two automated waste sterilizers process over 5 tons of regulated medical waste daily. Conveyors automatically transfer the treated wastes directly into waste compactors at the soiled docks. Hazardous wastes are held in special holding rooms and a special detection system interfaces to the AGVS robots to automatically segregate any cart that contains radioactive materials.
The soiled docks provide: two compactors for the collection of treated Medical Wastes and rubbish; one cardboard compactor; two open top containers arranged for side loading; two full sized truck docks for pickup of recycled wastes, hazardous wastes, soiled linens, etc.
Contact The Schachinger Group. (703) 608-2263
Our experience in providing services for more than 800 clients worldwide over 35 years has revealed the benefits of treating these important disciplines as interdependent functions, planned in a coordinated way with the assistance of one experienced and qualified firm.