Project Case Studies
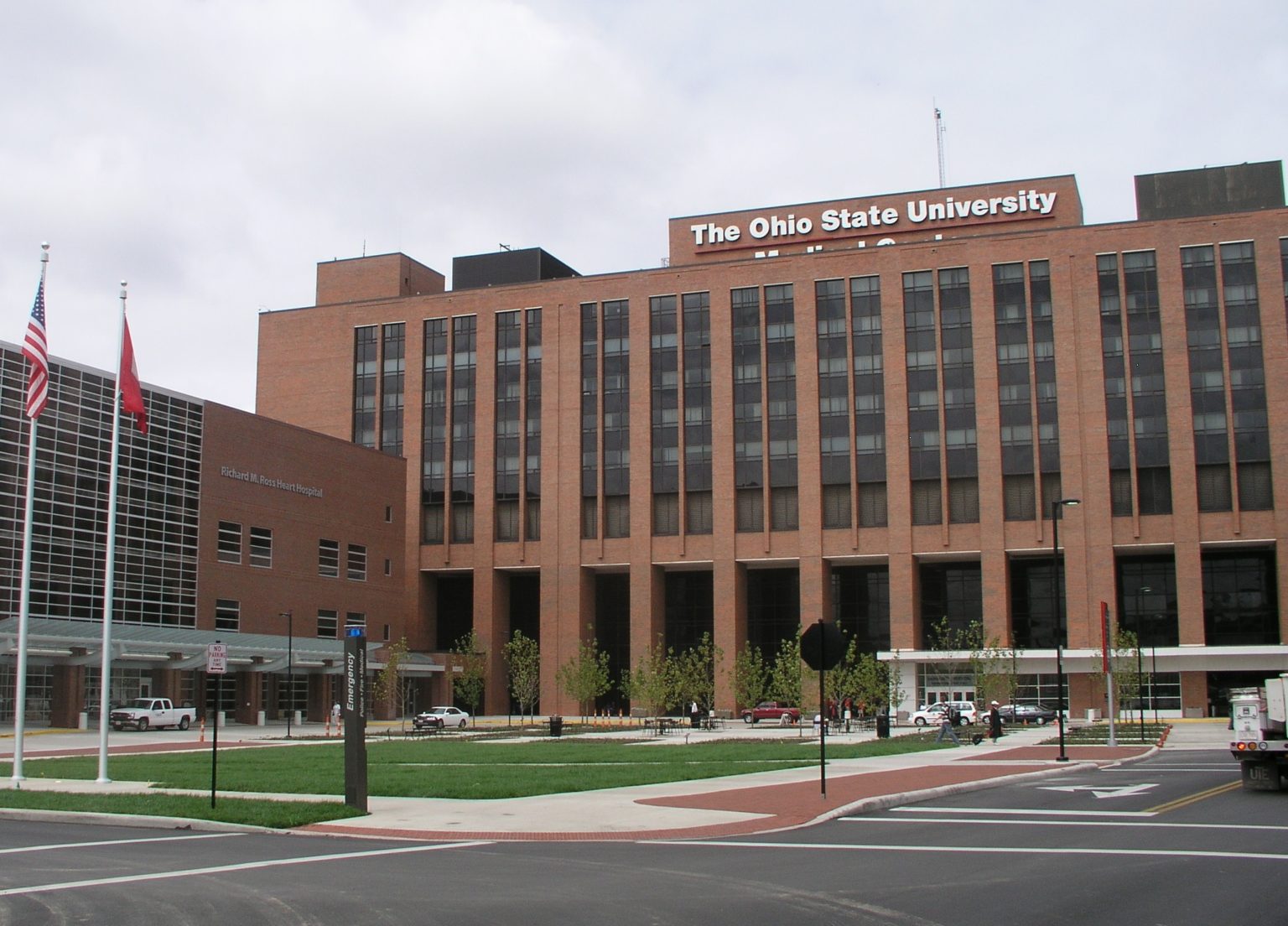
The Ohio State university Medical Center
Ohio State University Medical Center (OSUMC) is comprised of ~ 1,000 inpatient beds in five hospitals, clinics, academic and research facilities. OSUMC utilized an overhead rail material handling system for a number of years, supporting 1,620,424 gross square feet in several facilities.
In 1997, The Schachinger Group (TSG) performed detailed studies that projected needs for the transport of more than 2,300 carts daily. The cost of upgrades and then operating and maintaining the existing overhead rail cart system proved greater than any possible overall cost savings. Hence OSUMC initiated an in‐depth study of alternatives.
The Schachinger Group, Inc. (TSG) was retained to study and to lead the OSUMC Team’s efforts in ascertaining the most appropriate and efficient materials handling strategies.
Study Objectives.
Study objectives were to analyze current and foreseeable future materials handling requirements, to identify options, and to determine the best course of action. Four system alternatives were considered, including fully manual movement and a manually driven tow system. A new automated guided vehicle (AGV) system was determined to be the best alternative, saving over $65 million dollars over a 25 year period, when compared with all of the other alternatives studied. This was later verified in an independent study commissioned in 2002.
Implementation.
TSG provided detailed materials handling and transportation studies and analysis, updated functional and operational programs. TSG facilitated the reengineering of User Department processes and operations. TSG provided the detailed programming, design, specifications, bid, AGVS Vendor selection, Construction Administration and implementation assistance services. The process also uncovered the need and then the development, design and construction of a new 16,000 sf Central Sterile Processing Department.
To make‐the‐building‐ready for the new ATS system installation, a phased $3.5 million effort impacting 50 different areas in the Hospital, was required. Installation of the ATS was completed in 2004 with the following major components: 46 Automated Robots; 8 different cart types; 9 dedicated elevators; 2 automated cartwashers and various associated controls and devices.
Transporting carts and materials on the ATS Elevators reduced demand on existing patient and public elevators.
As a result, the typical response time for an elevator has decreased from ~4‐ ½ minutes to ~40 seconds. The ATS allows personnel to maximize the amount of time spent caring for patients, while providing a safer workplace.
The AGVS used 25,000 square feet less space than the manual system allowing that space to be used for other valuable functions.
Contact The Schachinger Group. (703) 608-2263
Our experience in providing services for more than 800 clients worldwide over 35 years has revealed the benefits of treating these important disciplines as interdependent functions, planned in a coordinated way with the assistance of one experienced and qualified firm.